Understanding Concrete Weight Plate Molds: A Comprehensive Guide
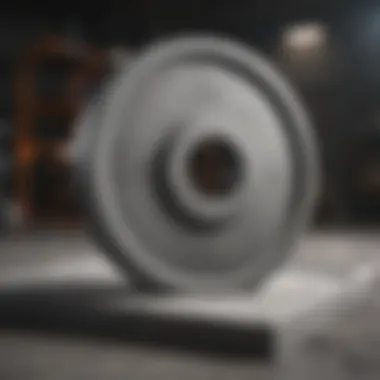
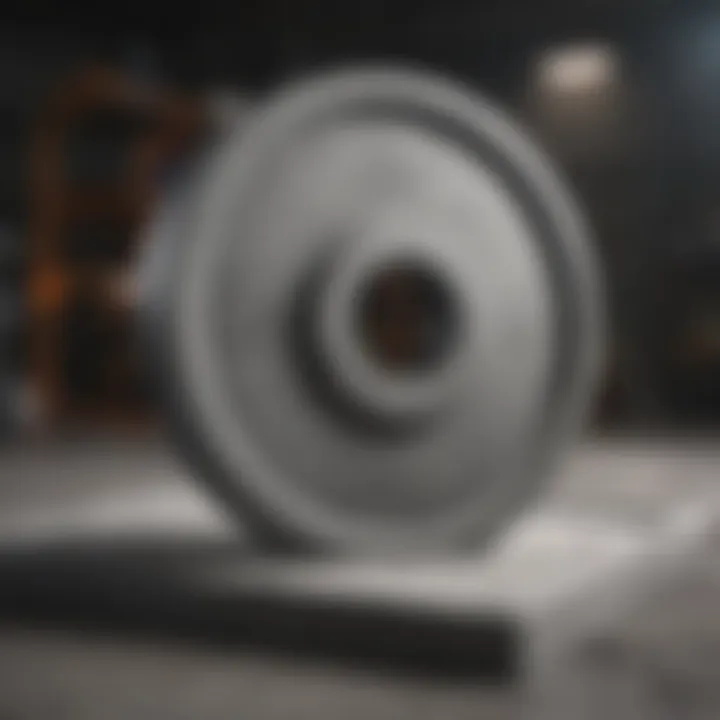
Intro
The fitness industry continually evolves, bringing forth innovations designed to enhance workout experiences. Among these innovations are concrete weight plate molds, a critical component in creating custom weight plates that suit diverse training needs. Whether for personal use or commercial production, understanding the significance of these molds is paramount. This segment provides an overview of concrete weight plate molds, outlining their relevance in fitness gear manufacturing and training efficacy.
Concrete weight plates serve as essential fitness accessories, contributing to strength training and overall fitness regimens. The incorporation of custom molds into the manufacturing process allows for tailored designs, which facilitate various workout intensities and techniques. This guide aims to elucidate the various facets of concrete weight plate molds, ensuring readers are equipped with comprehensive knowledge to enhance their training routines.
Health Benefits
Physical Health Benefits
Utilizing concrete weight plates in strength training provides several physical health benefits. Increased muscle mass is one of the most prominent advantages. As individuals engage in resistance training, the muscles respond by increasing in size and strength. This process also promotes fat loss, as muscle burns more calories than fat even in resting states.
Another notable benefit is improved bone density. Studies consistently show that weight-bearing exercises contribute to stronger bones, which can reduce the risk of fractures and osteoporosis, particularly in older adults. Concrete weight plates, characterized by their sturdy design, can effectively contribute to these weight-bearing exercises, making them a reliable option for enhancing bone health.
Strength training with concrete plates also promotes joint stability and flexibility. The progressive nature of resistance training encourages the body to adapt, leading to enhanced joint function and overall mobility.
Mental Health Benefits
The mental health benefits associated with strength training are equally important. Engaging in a structured workout routine can significantly reduce symptoms of anxiety and depression. The act of lifting weights, such as those made with concrete molds, releases endorphins that enhance mood and create a sense of well-being.
Moreover, the discipline required for regular training fosters improved focus and concentration. This mental fortitude can extend beyond the gym, positively impacting various aspects of life, including work and personal relationships. Strength training can also promote better sleep quality, which further contributes to mental health and cognitive function.
"Exercise is a powerful antidote to stress, anxiety, and depression, making it a crucial element in personal health routines."
Practical Tips
Choosing the Right Mold
When selecting concrete weight plate molds, itβs essential to consider a few factors:
- Material Quality: Ensure that the molds are made from durable materials to withstand repeated use.
- Design Variety: Look for molds that offer a range of plate weights to accommodate various fitness levels.
- Ease of Use: Molds should be user-friendly, allowing for straightforward pouring and demolding processes.
Effective Workout Routines
Employing the right concrete weight plates can enhance workout routines. Here are some recommended exercises:
- Deadlifts
- Squats
- Bench Press
- Overhead Press
Integrating these exercises with concrete weight plates ensures the muscles are targeted effectively, promoting strength gains.
By understanding the application and benefits of concrete weight plate molds, individuals can make informed decisions that enhance their fitness journey. Through thoughtful selection and utilization of these molds, one can cultivate a stronger body while reaping the associated mental health rewards.
Prelude to Concrete Weight Plate Molds
Concrete weight plate molds play a crucial role in the fitness equipment industry, particularly for individuals and facilities striving to enhance their weight training experiences. These molds not only dictate the shape and size of the weight plates but also influence various factors such as durability and customization. Understanding these molds is essential for fitness professionals, gym owners, and serious trainers who aim to tailor their equipment to specific training objectives.
What Are Concrete Weight Plate Molds?
Concrete weight plate molds are forms used to shape wet concrete into specific weights and sizes for workout plates. They are crucial in the production of homemade or custom weight plates. Generally, these molds come in various shapes, like standard round designs or specialized forms to meet specific training requirements. Using these molds, manufacturers can create plates that cater to the diverse needs of fitness enthusiasts. The essence of these molds is to facilitate the casting process, allowing for a wide range of weights and shapes, depending on what the user prefers.
The Importance of Molds in Fitness Equipment Production
The significance of molds in the manufacturing of concrete weights cannot be understated. They provide the framework within which concrete is poured and set, determining both the final product's functionality and aesthetic appeal.
- Consistency: Molds ensure that each weight plate produced can maintain the same dimensions and weight specifications, which is vital for athletes who rely on precise weights for their training.
- Customization: They allow for the production of unique shapes or weights tailored to specific exercises or strength training routines. This can enhance the user's training experience considerably.
- Cost-Effectiveness: In producing large quantities of concrete weights, using molds reduces material wastage and ensures that production costs remain low.
In summary, understanding the role of concrete weight plate molds is fundamental for anyone involved in fitness equipment manufacturing or those looking to enhance their weight training setups. The ability to customize and maintain quality in produced weight plates has a lasting impact on the user's training effectiveness.
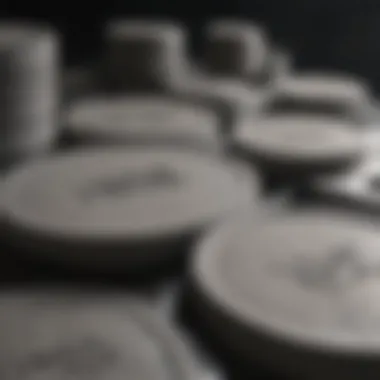
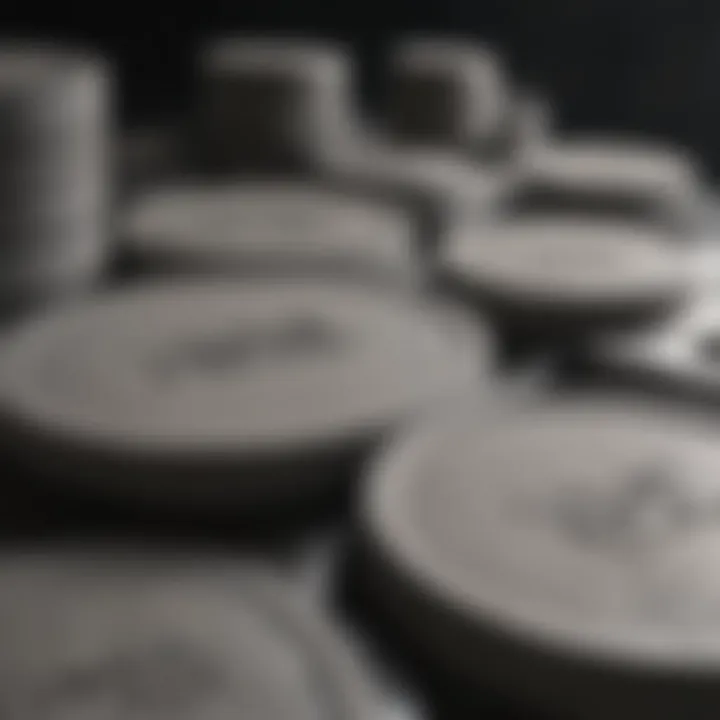
Types of Concrete Weight Plate Molds
The use of concrete weight plate molds is critical in the fitness industry. These molds play a vital role in how effective and versatile your weight training can be. Each type of mold serves a unique purpose, allowing for customization and functionality that can enhance individual workout goals. By understanding the various types of molds, users can make informed choices tailored to their specific training requirements. The benefits of using the right mold are far-reaching, impacting not just cost, but also the training experience itself.
Standard Round Molds
Standard round molds are perhaps the most common type of concrete weight plate mold. These molds are designed to produce circular weight plates of various sizes, typically ranging from five to fifty pounds. The simplicity of standard round molds allows for easy production, making them cost-effective for manufacturers. They provide a familiar weight plate shape that fits standard gym equipment, which is a significant advantage for many fitness enthusiasts.
- Easy to use and common in most gyms.
- Compatible with a wide range of barbells.
- Typically more economical to produce.
Standard round molds often allow for standardization in weight, meaning users can have a clear understanding of the weights they are lifting at all times. This can be especially important for beginners who are just getting started with their weight training journey.
Customized Shape Molds
Customized shape molds offer flexibility that standard molds cannot provide. These molds can be tailored to create weights that fit non-traditional dimensions or aesthetics. Fitness professionals and enthusiasts can benefit from the ability to produce weights that target specific training needs. For instance, one might create a weight plate in the shape of an animal or any other design to encourage kids to engage in exercise.
- Freedom to design weights that fit personal styles or training needs.
- Can incorporate unique gripping features for safety and ease of use.
- Potential for thematic designs, enhancing the appeal for particular audiences.
The choice to use customized shape molds can also have psychological benefits. Weight training often focuses on personal expression, and unique designs can help motivate individuals to engage with their fitness routines regularly.
Adjustable Weight Plate Molds
Adjustable weight plate molds are one of the more innovative developments in concrete weight plate production. They allow for the creation of plates whose weight can be modified after they are cast. This can be particularly useful for varied training sessions, as it eliminates the need for multiple plates. Users can simply add or remove weight as their training progresses.
- Ideal for those who want to progress slowly and steadily without buying new plates.
- Space-saving, as fewer weights are needed for different training stages.
- Flexibility to change weight quickly usually improves workout efficiency.
By utilizing adjustable weight plate molds, fitness enthusiasts can experience a more responsive training routine, allowing for gradual increases in strength with less equipment investment.
"The right mold choice can significantly shape the weight training experience and outcomes."
Materials Used in Concrete Weight Plate Molds
The selection of materials in the production of concrete weight plate molds plays a critical role in the quality and efficiency of the end product. The right materials not only affect the durability and longevity of the molds but also influence the overall weight and performance of the concrete plates themselves. Understanding the different materials used allows fitness enthusiasts and producers alike to make informed decisions that align with their training objectives and operational criteria.
Types of Concrete for Molds
When it comes to creating effective concrete weight plate molds, choosing the appropriate type of concrete is essential. Generally, there are three predominant types:
- Standard Concrete Mix: This is often used due to its accessibility and affordability. It provides good strength but may not be the best for extended outdoor use as it can deteriorate under adverse weather conditions.
- High-Performance Concrete: This type offers superior strength and durability. It is engineered for projects requiring additional resistance to wear and tear, making it suitable for heavier plates that will undergo rigorous use.
- Lightweight Concrete Mix: Ideal for those who may prefer lighter weight plates, this mix incorporates lightweight aggregates. This option is especially useful for those with specific training needs or for younger users.
Each mix has its own benefits and considerations, leading to varying results in both performance and cost.
Mold Materials: Pros and Cons
The materials used for constructing the molds themselves affect every aspect of the final concrete weight plates. Here is a brief overview of some common mold materials and their respective advantages and disadvantages:
- Plastic Molds: Pros: Lightweight, resistant to corrosion, and can be easily shaped. Cons: May not provide the best durability over time compared to metal.
- Steel Molds: Pros: Highly durable and capable of withstanding repeated use without deforming. Cons: Heavier and can be more costly to produce.
- Aluminum Molds: Pros: Lighter than steel and provides a good balance between durability and cost. Cons: Can dent or scratch more easily than steel.
- Fiberglass Molds: Pros: Can be molded into complex shapes and provide excellent release properties. Cons: Typically more expensive and may not be as durable as metal options.
Choosing the right mold material greatly influences the usability and functional quality of the concrete weight plates.
In summary, the materials used in concrete weight plate molds carry significant implications for product durability and functionality. Careful selection based on the intended use, cost factors, and specific training requirements can enhance user experience and satisfaction in weight training activities.
Manufacturing Process of Concrete Weight Plates
The manufacturing process of concrete weight plates is fundamental to understanding their quality and performance. This process encompasses several critical stages, each contributing significantly to the final product's durability and usability. By comprehending these steps, fitness enthusiasts and professionals can make informed decisions about the equipment they choose.
Designing the Mold
Designing the mold is the first step in creating concrete weight plates. This phase involves careful planning to ensure the mold meets specific requirements aimed at achieving desired objectives. Factors such as the thickness, diameter, and shape of the mold must be considered. The design must also account for ease of use during the pouring and demolding processes.
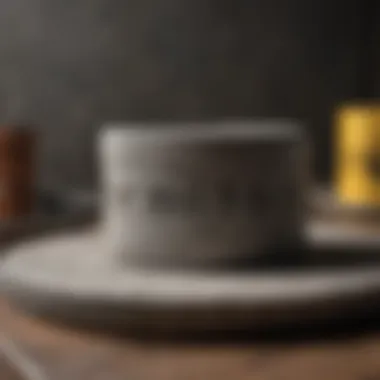
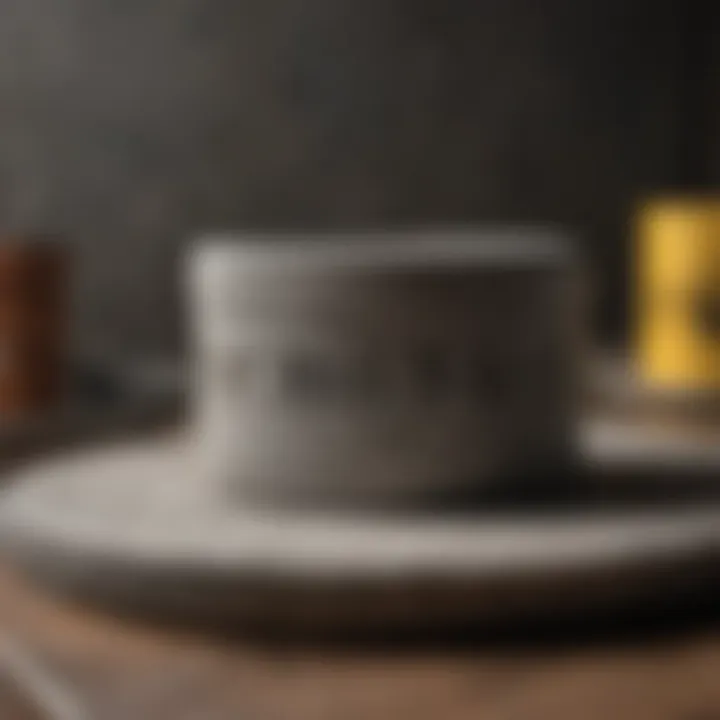
In this stage, materials play a crucial role. Common choices for molds include steel and high-density plastic, both of which offer different benefits. Steel is often preferred for its strength and longevity, while plastic may be lighter and easier to handle.
The design phase is also when modifications can be made to cater to unique training needs. For instance, a trainer could customize a mold for a more ergonomic grip or a specific weight distribution. This tailored approach can enhance the userβs workout experience by providing a more natural and intuitive feel during exercises.
Pouring Concrete into the Mold
Once the mold is ready, the next step is pouring concrete into it. This activity requires precision and care. The mix formulation must be suitable for weight plates, usually a blend that maintains strength while minimizing cracking during the curing phase. Using proper techniques during the pour is essential to avoid air pockets or inconsistencies in the weight distribution.
It is beneficial to vibrate the mold gently after pouring. This vibration helps to eliminate air bubbles that can weaken the structure of the weight plate. Additionally, careful attention should be paid to the environmental conditions while pouring. For example, extreme temperatures can adversely affect the curing process, ultimately impacting the integrity of the finished product.
Curing and Finishing Stages
The curing stage is vital to ensuring the strength and durability of the concrete weight plates. It typically spans several days to allow the concrete to achieve its full strength. During curing, it is essential to maintain moisture in the mold, which can be done using damp cloths or plastic sheeting. This step prevents the concrete from drying out too quickly, which can lead to cracks and weakened structures.
After the curing period, the finishing stage comes into play. This involves removing the mold carefully to avoid damaging the freshly cured plate. Depending on the complexity of the mold, this process may need specialized tools or techniques.
Finishing can also include sanding or smoothing off any rough edges, ensuring safety and improving the aesthetic appeal. Final inspections check for any defects, ensuring that only quality products are ready for use. The goal is to have plates that are not only functional but also visually appealing to users.
Benefits of Using Concrete Weight Plates
The use of concrete weight plates in fitness training offers several advantages that contribute both to the effectiveness of workouts and the cost of equipment. Understanding these benefits is crucial for health professionals, wellness coaches, and fitness trainers as they guide individuals towards achieving their fitness goals. The three key aspects include cost-effectiveness, customization options for specific training needs, and the durability of the materials used. Each of these factors plays a pivotal role in deciding whether concrete weight plates are the right choice for a fitness regimen.
Cost-Effectiveness
Concrete weight plates are often more affordable compared to plates made from other materials, such as iron or rubber. This is primarily due to the low cost of raw materials needed to produce concrete. For individuals or small gyms with limited budgets, choosing concrete weight plates can offer significant savings, allowing them to allocate funds to other essential pieces of equipment.
- Material Savings: Concrete is easier to source than metals, which helps lower production costs.
- Simplicity of Production: The process of making concrete plates is less labor-intensive than that of traditional weight plates.
- Long-Term Investment: When properly maintained, concrete weights can last a long time, reducing the need for frequent replacements.
Customization for Training Needs
One of the most appealing features of concrete weight plates is the ability to customize them according to training requirements. This adaptability allows fitness enthusiasts to tailor their equipment to meet specific goals, whether building strength, enhancing endurance, or perfecting form.
- Weight Variability: Trainers can adjust the weight according to the level of fitness or specific workout requirements. This is essential for progressive strength training.
- Shape and Size Options: Users can create plates in various shapes and sizes to better fit their training routines, allowing for innovative workout designs.
- Personal Branding: Fitness enthusiasts can personalize their weights with colors, designs, or logos, making them unique and distinct.
Durability and Longevity
Concrete weight plates are known for their impressive durability. The inherent nature of concrete makes it resistant to wear and tear when properly cured and handled. Unlike rubber weights, concrete plates do not degrade as quickly under heavy use.
- Resistance to Environment: Concrete weight plates can withstand exposure to varying weather conditions without degrading, allowing for both indoor and outdoor training flexibility.
- Scratch and Chip Resistance: While concrete may chip if dropped from significant heights, regular use will not result in significant scratching, ensuring they maintain their integrity over time.
- Maintenance Simplicity: Cleaning concrete plates is straightforward, requiring only a wipe down with water or a mild detergent to keep them in good shape.
Concrete weight plates not only provide cost savings but also offer flexibility and durability, making them a wise choice for serious fitness enthusiasts.
Best Practices for Using Concrete Weight Plate Molds
Using concrete weight plate molds effectively can enhance the quality and utility of the weights produced. Following best practices not only ensures a good end product but also extends the lifespan of the molds themselves. Awareness of specific maintenance routines, safety protocols during the manufacturing process, and proper curing techniques is essential for anyone involved in the production of these weights.
Proper Maintenance of Molds
Regular maintenance of concrete weight plate molds is crucial to ensure their longevity and functionality. Over time, molds can become damaged or worn, leading to imperfections in the concrete plates produced. Here are some maintenance practices to consider:
- Clean After Each Use: Remove any residual concrete left in the molds after a session. This helps prevent buildup that can cause defects.
- Inspect for Damage: Regularly check molds for cracks or wear. Small issues can escalate if not addressed soon.
- Use Mold Release Agents: Applying a mold release agent can reduce friction and facilitate the easy removal of concrete plates, thus minimizing mold wear.
Maintaining molds increases productivity and reduces costs associated with repairs or replacements.
Safety Considerations During Pouring
Safety is paramount when pouring concrete into molds. The process can involve several risks such as exposure to dust, heavy lifting, and even chemical hazards depending on the materials used. Consider the following safety measures:
- Personal Protective Equipment (PPE): Always wear gloves, eye protection, and a dust mask.
- Training for Handling Materials: Ensure that anyone involved in the process understands how to safely manage concrete and related materials.
- Avoid Overloading: Do not exceed the weight capacity of the molds. Overloading can lead to mold failure or accidents.
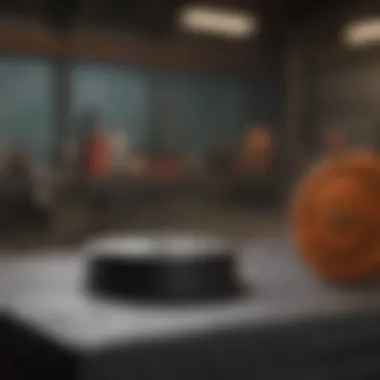
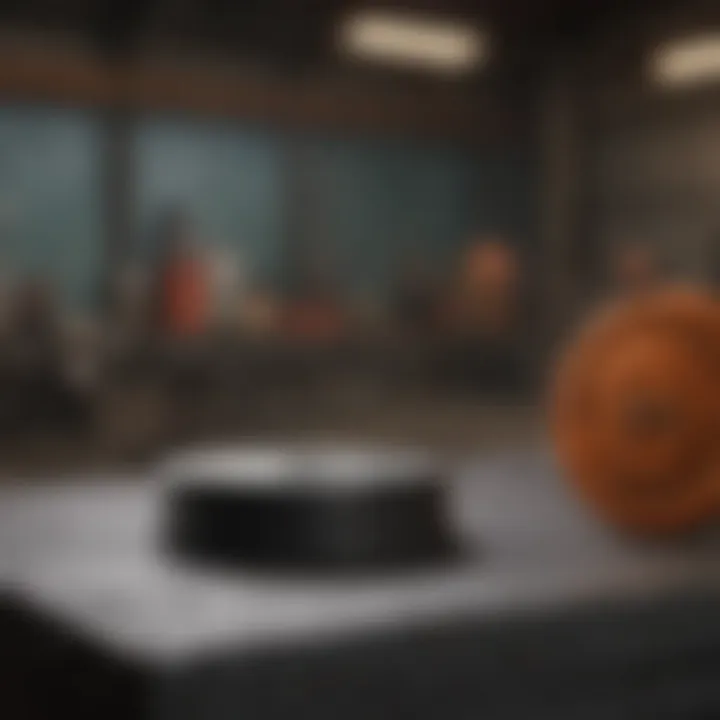
These practices help mitigate risks, preventing injuries and ensuring a smooth pouring operation.
Ensuring Proper Curing Techniques
Curing is a critical step in the concrete weight plate production process. It affects the strength and durability of the final product. Adhering to proper curing techniques can lead to significant improvements in weight quality. Here are key considerations:
- Maintain Moisture Levels: Keep the concrete moist for at least 24 hours after pouring. This helps in achieving the best hydration.
- Control Temperature: Ideally, the curing environment should be between 10Β°C to 30Β°C (50Β°F to 86Β°F). Extreme conditions can adversely affect curing.
- Use Curing Compounds: Applying curing compounds can help seal moisture, ensuring consistent curing.
Implementing these techniques can enhance the structural integrity of concrete plates, making them safer and more reliable for users.
Selecting the Right Mold for Your Needs
Choosing the appropriate mold for concrete weight plates is crucial. This choice can directly affect training effectiveness and safety. Molds are not just containers; they determine the shape, weight, and overall usability of the concrete plates. Selecting the right mold involves careful consideration of several factors, each contributing to an enjoyable and productive workout experience.
Assessing Your Training Goals
Before deciding which mold to use, itβs essential to define specific training goals. Different exercises require different weights and shapes. For instance:
- Strength Training: If the primary focus is on building muscle strength, standard round molds may suffice, as they provide balanced weight distribution.
- Functional Training: Customized shape molds can be beneficial for exercises that target specific movements.
- Weightlifting Competitions: For competitors, adherence to official dimensions may require specialized molds that meet exact specifications.
Additionally, considering the weight range needed is important. If the goal is to support progressive overload, adjustable molds can provide the necessary flexibility. This adaptability ensures that you can easily increase the weight as training intensity grows. Ultimately, knowing your training objectives helps in making an informed choice for molds that best fit those needs.
Considerations for Home Gym Setups
Installing concrete weight plates in a home gym demands unique considerations. The available space, fitness goals, and desired equipment shape all play important roles. Here are key points to keep in mind:
- Space Limitations: If space is small, consider using stackable or adjustable molds that minimize footprint while providing versatility in weight adjustment.
- Design Aesthetics: The look of the weight plates may matter, particularly if the gym is part of a living area. Customized molds could offer designs that integrate better with home decor.
- Durability Concerns: At home, weight plates will endure frequent use. Selecting molds made of durable materials ensures longevity, critical for sustained fitness practices.
By factoring in these elements, choosing the right mold can transform a home gym into a highly functional training environment. These considerations enable you to make selections that enhance performance and uphold safety.
Innovations in Concrete Weight Plate Mold Design
Innovations in the design of concrete weight plate molds play a crucial role in the evolution of fitness equipment. As the fitness industry continues to grow, there is an increasing demand for more efficient and diverse training aids. Mold design significantly influences not only the quality of the final product but also impacts factors such as production efficiency, cost-effectiveness, and user customization. This section will explore essential advancements in this area, offering insights into their benefits and practical applications.
Advancements in Material Technology
With ongoing research and development, material technology for concrete weight plate molds has seen remarkable progress. The use of durable and resilient materials, such as high-density polyethylene, ensures that molds can withstand repeated use without wear and tear. These materials also enhance the mold's longevity, allowing manufacturers to produce high-quality products with less waste.
Modern mold designs often incorporate modular systems. This innovation enables users to adjust the size and shape of the molds, accommodating different weight requirements and user preferences. Such flexibility allows for the production of customized weight plates that align with specific training goals.
Additionally, advancements in 3D printing technology are revolutionizing mold design. These techniques allow for precise and complex shapes that were previously unattainable. It enables manufacturers to prototype and iterate designs quickly, reducing lead times for production.
Incorporating various additives can improve the concrete's performance within these molds, such as increasing strength and reducing water permeability. This further enhances the overall quality of the weight plates produced.
Eco-Friendly Mold Options
The growing awareness of environmental concerns is influencing mold design significantly. Innovations in eco-friendly materials are gaining traction within the concrete weight plate mold industry. Manufacturers are increasingly exploring alternatives like recycled plastics and biodegradable composites. These materials not only reduce environmental impact but also cater to a market looking for sustainable fitness solutions.
The use of eco-friendly molds can lead to less energy consumption during manufacturing. Using renewable resources or recycled materials lowers carbon footprints and can appeal to ethically-minded consumers.
Moreover, technology that incorporates less aggressive chemical treatments during the mold-making process can further enhance sustainability. Reducing the use of harmful substances will benefit both the environment and the health of workers involved in the manufacturing process.
In summary, innovations in mold design - particularly in terms of material technology and eco-friendly options - are reshaping the concrete weight plate industry. These advancements bring numerous benefits, including enhanced performance, durability, and environmental sustainability, ultimately leading to better training experiences for users.
"The shift towards sustainable materials and advanced technology is not just an industry trend; it is a fundamental transformation that supports better health and environmental responsibility."
Continued exploration in these areas will drive further innovations, presenting exciting opportunities for the future of weight training equipment.
Epilogue
In this article, we have explored the nuanced aspects of concrete weight plate molds, delving into their significance in fitness equipment manufacturing. The insights presented here aim to arm health professionals, wellness coaches, and fitness trainers with a deeper understanding of how to effectively integrate these molds into weight training practices.
The Future of Concrete Weight Plate Molds
As the fitness industry evolves, so does the technology surrounding concrete weight plate molds. There is a noticeable trend towards sustainability, with an increasing number of manufacturers focusing on eco-friendly mold options. This shift is crucial as more consumers demand environmentally responsible fitness products that do not compromise on quality or performance. Innovations in material technology also play a vital role. Advancements such as lightweight composites and enhanced durability measures help to produce molds that are both efficient and robust. These future directions not only improve the manufacturing process but also enhance the overall workout experience for users.